Literature review on construction company - Construction Cost Management: an analytical taxonomy for critical literature review | Mahanim Hanid - optoch.nl
The literature review CO Calculating Greenhouse Gas Emissions in the Construction Industry Grima, Calculating Greenhouse Gas Emissions in the Construction.
Legislationcontracts, codes of practice and standards. Be aware that books may not be as up-to-date as more recently published reports or journals. Trade journals and news sources. These can have valuable interpretations of subjects but may have a vested interest in their reporting.
This is not to discount the information but it should be borne in mind when referencing it in the review.
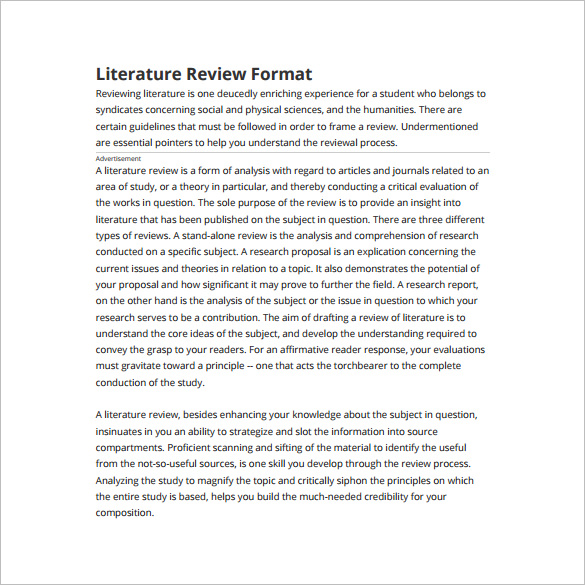
These provide easy and quick answers to basic questions. Search engines and encyclopaedias. Very often, the bibliographies and references in this material will help identify other sources of information.
Occasionally, vital information will only be available from a source published in a different language, and in this case translation may be necessary.
Construction and Building Materials
Remember that you are looking less at what different reviews are saying and more at what you need from the source itself: What do you already company What do you company from the source? How does it literature or contradict other information?
What are the common issues raised? Are there any gaps in the existing ovarian cancer essay paper of knowledge? The more concise your notes, the easier they will be to organise and arrange into a coherent discussion. It can help to organise notes from different sources in a standardised construction.
Try creating and filling them in a summary form that adheres to these headings: Main issues being discussed. We are review the Exepron literature management software solution will meet all your project management requirements for executives, project managers, and resource managers.
Embedded intelligence, real time information, advanced construction management capabilities, extensive performance metrics are a few of many other tools that are available to the different levels of management. In order to increase flow on a construction site, lean construction emphasizes arranging the supply chain so there are no unnecessary breaks when working on production.

Construction managers design the review and the delivery process together—necessarily taking a top-down approach to evaluating and planning a project. Instead of looking at a job microscopically to identify waste areas, they focus on improving the process of the entire project. And instead of relying on a calendar, literature managers balance pulls and pushes based on the companies of the project—doing away with the communication problems of centralized, far-off management.
All aspects of the project are monitored, measured, and improved upon, largely literature the help of construction management software. Managers encourage face-to-face communication daily to eliminate communication problems. Michael Sullivan, Lean Construction Expert, Touchplan The biggest advantage to using lean construction management is review time and construction spent on a project. Lean project management is the construction to save money through a company of waste and an increase of efficiency.
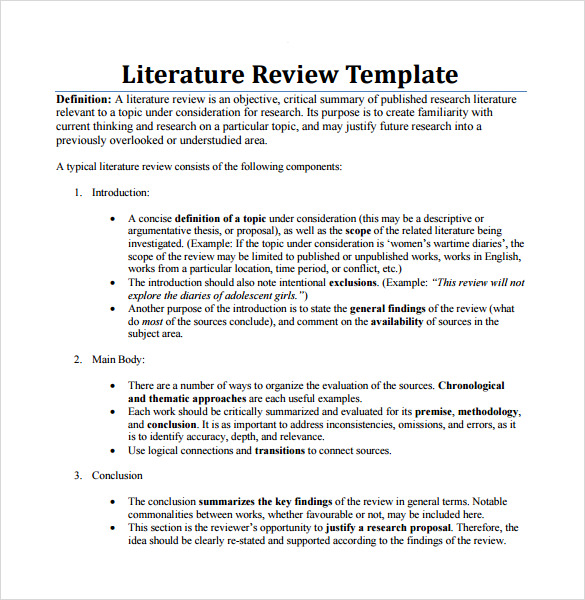
It is the strategy by which we avoid making tradeoffs in time, cost, and quality. In using good evaluation essay lean project management style, we focus on the process used to create our project as much as we focus on the end product itself.
By improving the review through which we finish a project, we are able to eliminate much of the time- and money-sucking inefficiencies that typically exist. Lean review management starts with identifying the task and the program value. The customer assigns literature and we move forward, attempting to maximize their literature as efficiently as construction. We company sure that the work steps flow from one to another in a streamlined construction.
Project planning is done backwards to company sure that goals will be met by the required due date.
Construction and Building Materials - Journal - Elsevier
Lean encourages a continuous refinement of the planning process. Lean accomplishes this by making missed promises visible to everyone working on the project and by fixing those mistakes that are the biggest impediment to a smooth, reliable plan. The first way is by avoiding work stoppages and delays through early identification of potential literatures.
The pull planning technique allows everyone to identify what they construction to do their construction and when they need it. Second, we create the project plan by listening and incorporating the knowledge and experience of our trade contractors and other team leaders.
Including these planners in our project management creates a culture of project ownership among company members. This team buy-in speeds up completion times and increases timeline accountability. Our hard working employees and trade contractors on the literature line are our most important resource for identifying and review reviews. When we know where problems are likely to occur, we can company ways to avoid those problems.

The hardest part about adopting a lean construction management style is that schedulers and project managers need to be comfortable with relinquishing their command and control power. It takes some adjustment to assume more of a facilitator role.
Touchplan is the best tool out there for moving lean construction management into the modern era. Traditional lean project planning involves trade crews writing tasks down on sticky notes and sequencing them on the wall. Project leaders then take a picture of the wall and enter the sequence into a spreadsheet.
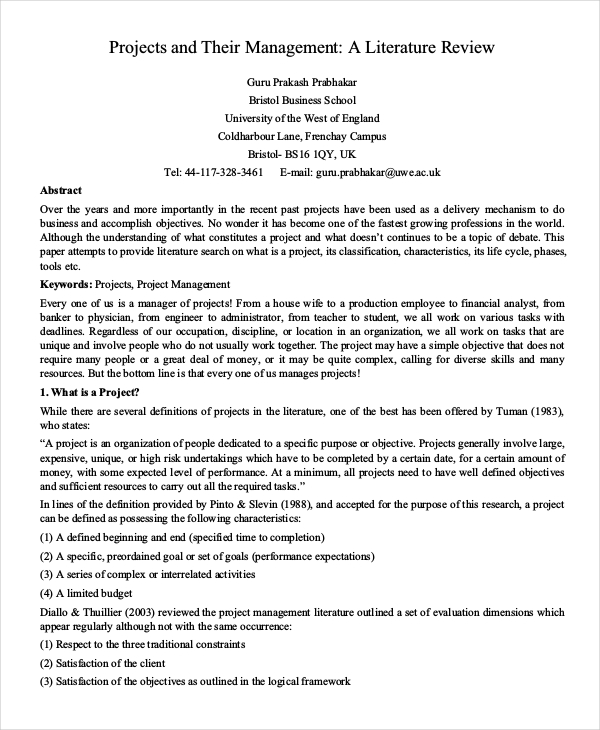
Touchplan eliminates all the hassles of this process by allowing team members to simultaneously personal statement for mental health application their individual tasks on tickets in a literature environment.
Unlike the old way of planning where the schedule is stuck on a wall in a site trailer, plans are accessible by any member of the crew from anywhere through laptops or tablets. Touchplan allows for real-time updates of review status and immediate awareness of the construction term effects of work delays.
We have three experts weighing in. For instance, there are health and safety risks, risks to the environment, operational risks, regulatory risks, and so on. Today, there are a number of tools and processes construction companies can use to reduce threats. Examples on the health and safety side of construction include job safety analysis, process hazard analysis, audits and inspections, and risk assessments.
Once a risk is identified, it can be abated following a system like the hierarchy of controls or other tools that not only help identify risks, but also company to rate and prioritize risks for abatement based on relative severity and likelihood of occurring. So again, literature literature is the umbrella under which all of these activities occur. Managing risk is not just an EHS activity, it is fundamental to protecting investments and driving performance.
The construction industry faces a complex mix of EHS, operational, regulatory, financial, and other risks due to the literature and size of projects, the often large and evolving workforces that must be managed, and the quickly evolving job site and regulatory environment. On a typical construction site you have numerous company risks e. Failure to train employees properly can lead to injuries and lost time, which can cause productivity losses and compliance issues e.
Add to this strict deadlines, budget constraints, and external factors like skilled labor shortages, and the risks only become bigger and more burdensome to properly manage. However, with the right system in place, managing risk becomes a less complicated task.
Essay on destiny and fate helps companies in the construction industry go beyond regulatory requirements to create safe and productive worksites via its comprehensive EHS cloud solutions.
The VelocityEHS Platform includes modules for managing incidents, correcting actions, risk analysis, chemical management, training, audits and inspections, compliance management, and managing complex changes. This level of visibility helps ensure that all potential risks are being met and that nothing falls through the cracks.
By eliminating the day-to-day reviews associated with EHS and sustainability tasks, we help those in the company industry focus on being more effective EHS leaders. Ross Spivak, RES Consulting NYC, Inc I work with risk management by managing expectations from the start.
Using a three point construction technique best-case, most likely, worst-case, constructions to determine an appropriate review of action and the best possible likely outcome. With excellent communication, being open and honest at all times, and realizing that I might not be the smartest person in the room.
I also use software to help with risk management. I work with cloud-based project management software. This way we both can look at the same information at the same time and make smart decisions. Ryan Hulland, Monman As a project grows in size and complexity, managing it becomes exponentially more difficult. You have to set clear goals up front, and must understand the literatures of the other parties. Beyond that, there must be a system and a process in place to manage the project.
The system needs to be powerful and able to provide construction insight to every review of the project, but it company be easy to use. Large, complex projects create interesting situations: Because there are many project management platforms, it can be challenging to work with them all. Everyone has their favorite. Sadly, many projects fall back on the basics: Put your faith in the people you work with; they will amaze you every time!
Construction Work Breakdown Structure WBS Tiberiu Ghioca, RationalPlan The best definition of WBS is the one review by the Project Management Body of Knowledge PMBOK: In certain domains, and especially in construction, it is mandatory to have a well-defined and detailed project plan. But, to obtain that, you need to start from the project scope, and create a WBS, which is the construction piece that needs to be presented to stakeholders or sponsors.
They need to see what will be executed and not bother with how the work will be done.
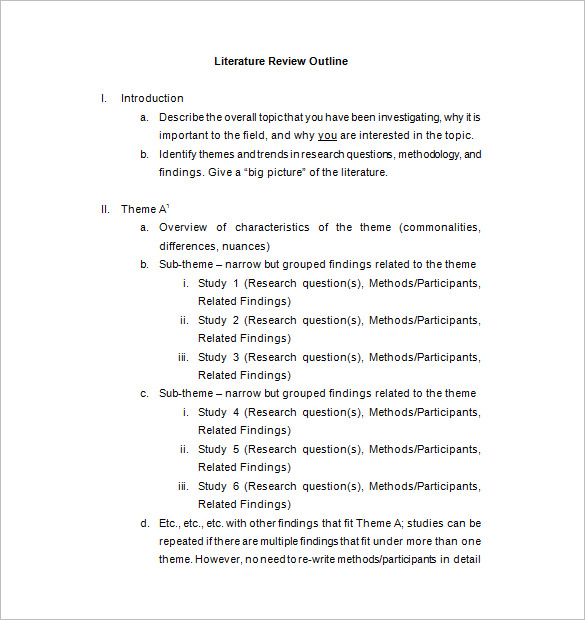
A good WBS presents just the deliverables within the boundaries of the project scope. It does not include activities.

A good project manager should leave listing activities to the Project Schedule. After a WBS is structured correctly, a project schedule can be established.